Destylacja rozpuszczalników to proces, który polega na oddzieleniu składników mieszaniny na podstawie różnicy ich temperatur wrzenia. W praktyce oznacza to, że podczas podgrzewania cieczy, składniki o niższej temperaturze wrzenia parują jako pierwsze, a następnie skraplają się w chłodniejszej części aparatury destylacyjnej. Kluczowym elementem tego procesu jest zastosowanie odpowiednich urządzeń, takich jak kolumna destylacyjna, która umożliwia wielokrotne skraplanie i parowanie, co zwiększa czystość uzyskiwanego produktu. Warto zaznaczyć, że skuteczność destylacji zależy od różnicy temperatur wrzenia poszczególnych składników oraz od ciśnienia atmosferycznego. W przypadku destylacji pod ciśnieniem atmosferycznym, temperatura wrzenia substancji jest wyższa niż w warunkach obniżonego ciśnienia, co może być korzystne dla substancji wrażliwych na wysoką temperaturę.
Jakie są najczęściej stosowane metody destylacji rozpuszczalników
W kontekście destylacji rozpuszczalników wyróżnia się kilka metod, które są dostosowane do specyfiki danej mieszaniny oraz wymagań dotyczących czystości końcowego produktu. Najpopularniejszą metodą jest destylacja prosta, która sprawdza się w przypadku substancji o znacznej różnicy temperatur wrzenia. W sytuacjach, gdy składniki mają zbliżone temperatury wrzenia, stosuje się destylację frakcyjną. Ta metoda polega na wykorzystaniu kolumny frakcyjnej, która pozwala na wielokrotne skraplanie i parowanie, co prowadzi do lepszego rozdzielenia składników. Inną techniką jest destylacja azeotropowa, która ma na celu rozdzielenie mieszanin tworzących azeotropy – substancji, które parują w stałych proporcjach niezależnie od składu cieczy. W przypadku bardziej skomplikowanych mieszanin można zastosować również destylację z użyciem rozpuszczalników wspomagających lub ekstrakcji cieczy.
Jakie są zastosowania destylacji rozpuszczalników w przemyśle
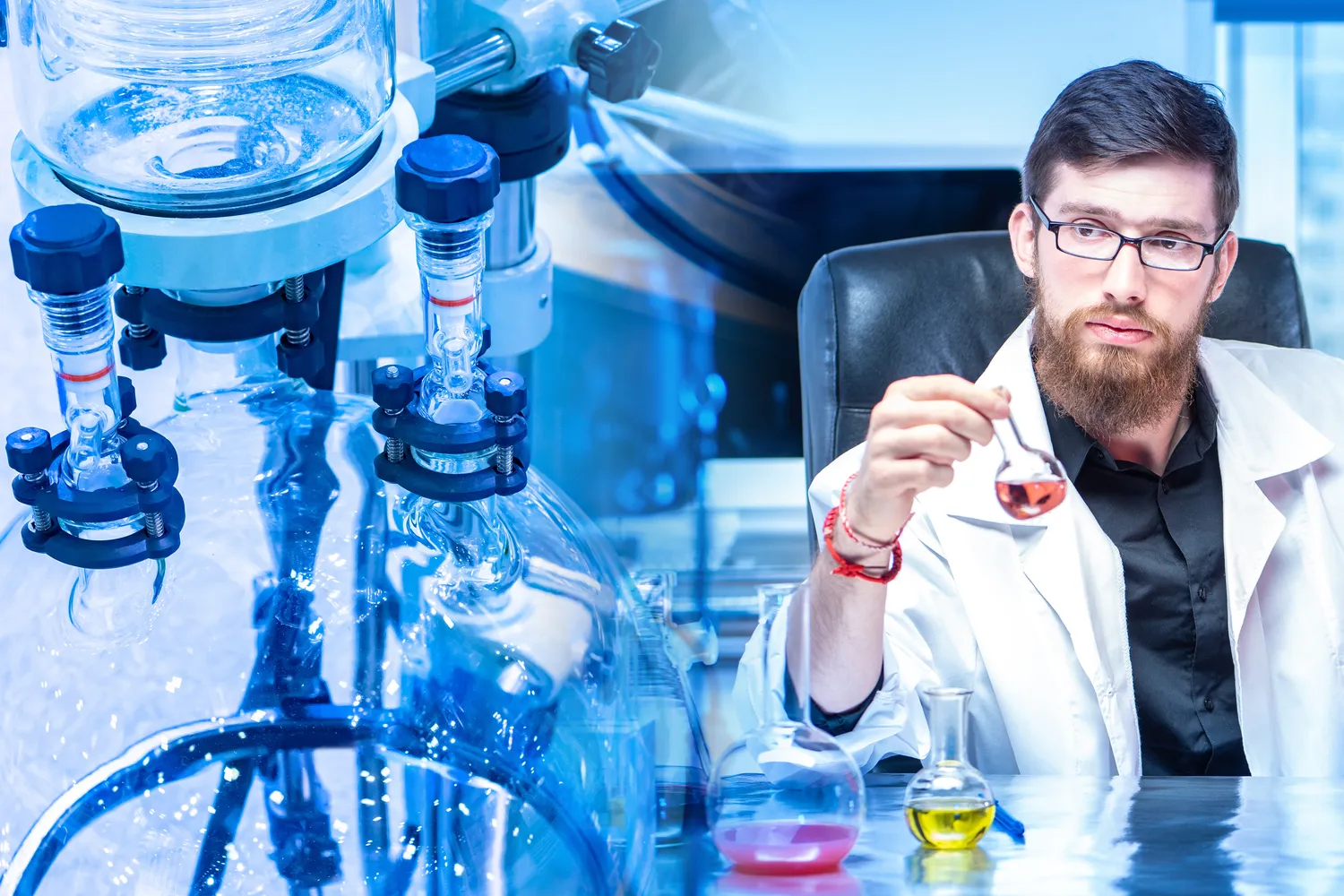
Destylacja rozpuszczalników znajduje szerokie zastosowanie w różnych gałęziach przemysłu, co czyni ją kluczowym procesem technologicznym. W przemyśle chemicznym jest wykorzystywana do oczyszczania surowców oraz produkcji wysokiej jakości chemikaliów. Przykładem może być produkcja alkoholi etylowych czy estrów, gdzie czystość rozpuszczalników ma bezpośredni wpływ na jakość końcowego produktu. W przemyśle farmaceutycznym destylacja odgrywa istotną rolę w procesie oczyszczania substancji czynnych oraz ich prekursorów. Dzięki temu możliwe jest uzyskanie leków o wysokiej skuteczności i bezpieczeństwie stosowania. Ponadto w przemyśle petrochemicznym proces ten jest kluczowy dla separacji różnych frakcji ropy naftowej, co pozwala na produkcję paliw oraz innych produktów chemicznych. Destylacja jest także wykorzystywana w produkcji kosmetyków oraz środków czyszczących, gdzie czystość składników ma ogromne znaczenie dla jakości i bezpieczeństwa produktów końcowych.
Jakie są korzyści wynikające z używania destylacji rozpuszczalników
Korzyści płynące z zastosowania destylacji rozpuszczalników są liczne i znaczące zarówno dla producentów, jak i dla konsumentów. Przede wszystkim proces ten umożliwia uzyskanie wysokiej czystości substancji chemicznych, co jest kluczowe w wielu branżach przemysłowych. Czyste rozpuszczalniki są niezbędne do produkcji leków oraz chemikaliów przemysłowych o określonych właściwościach fizykochemicznych. Kolejną zaletą jest efektywność energetyczna tego procesu – nowoczesne systemy destylacyjne są zaprojektowane tak, aby minimalizować straty energii oraz maksymalizować wydajność separacji składników. Dodatkowo możliwość recyklingu rozpuszczalników po ich oczyszczeniu przyczynia się do zmniejszenia kosztów produkcji oraz ograniczenia negatywnego wpływu na środowisko naturalne. Stosowanie destylacji pozwala także na dostosowanie procesu do specyficznych potrzeb danego przemysłu czy produktu, co zwiększa elastyczność produkcji.
Jakie są najważniejsze wyzwania związane z destylacją rozpuszczalników
Destylacja rozpuszczalników, mimo swoich licznych zalet, wiąże się również z pewnymi wyzwaniami, które mogą wpływać na efektywność i jakość procesu. Jednym z głównych problemów jest konieczność precyzyjnego zarządzania temperaturą oraz ciśnieniem w systemie destylacyjnym. Niewłaściwe ustawienia mogą prowadzić do niepełnego rozdzielenia składników, co skutkuje obniżoną czystością uzyskiwanych produktów. Ponadto, w przypadku mieszanin o zbliżonych temperaturach wrzenia, proces destylacji może być czasochłonny i wymagać zastosowania skomplikowanych urządzeń, takich jak kolumny frakcyjne. Innym wyzwaniem jest konieczność monitorowania i kontrolowania emisji substancji lotnych do atmosfery, co ma kluczowe znaczenie dla ochrony środowiska. Wiele rozpuszczalników jest toksycznych lub szkodliwych dla zdrowia, dlatego ich odpowiednie zarządzanie oraz recykling stają się priorytetem w nowoczesnych zakładach przemysłowych. Dodatkowo, zmiany w przepisach dotyczących ochrony środowiska oraz bezpieczeństwa pracy mogą wymuszać na producentach dostosowanie procesów technologicznych do nowych norm, co wiąże się z dodatkowymi kosztami i inwestycjami.
Jakie są innowacje w dziedzinie destylacji rozpuszczalników
W ostatnich latach obserwuje się dynamiczny rozwój innowacji w dziedzinie destylacji rozpuszczalników, co ma na celu zwiększenie efektywności procesów oraz minimalizację ich wpływu na środowisko. Jednym z kierunków rozwoju jest zastosowanie nowoczesnych materiałów konstrukcyjnych w budowie kolumn destylacyjnych, które pozwalają na lepsze zarządzanie przepływem cieczy oraz pary. Dzięki temu możliwe jest osiągnięcie wyższej wydajności separacji składników przy mniejszych stratach energii. Kolejnym przykładem innowacji są technologie wykorzystujące sztuczną inteligencję oraz zaawansowane algorytmy do optymalizacji procesów destylacyjnych. Dzięki analizie danych w czasie rzeczywistym możliwe jest szybkie dostosowywanie parametrów procesu do zmieniających się warunków, co przekłada się na lepszą jakość produktów końcowych. Warto również zwrócić uwagę na rozwój metod alternatywnych do tradycyjnej destylacji, takich jak ekstrakcja cieczy czy membranowa separacja, które mogą być bardziej efektywne w przypadku niektórych mieszanin chemicznych. Innowacje te mają na celu nie tylko poprawę efektywności procesów, ale także zmniejszenie zużycia surowców oraz ograniczenie negatywnego wpływu na środowisko naturalne.
Jakie są różnice między destylacją a innymi metodami separacji
Destylacja rozpuszczalników to jedna z wielu metod separacji składników mieszanin chemicznych, jednak różni się od innych technik pod względem zasad działania oraz zastosowań. W przeciwieństwie do filtracji czy sedymentacji, które opierają się na różnicy gęstości lub wielkości cząsteczek, destylacja wykorzystuje różnice temperatur wrzenia składników. To sprawia, że jest szczególnie skuteczna w przypadku cieczy o różnych właściwościach fizykochemicznych. Kolejną popularną metodą separacji jest ekstrakcja cieczy, która polega na wykorzystaniu rozpuszczalnika do wydobycia określonych składników z mieszaniny. Ekstrakcja może być bardziej efektywna w przypadku substancji o niskich temperaturach wrzenia lub w sytuacjach, gdy składniki tworzą azeotropy. Z kolei chromatografia to technika separacyjna oparta na różnicy w powinowactwie składników do fazy stacjonarnej i ruchomej. Jest to metoda niezwykle precyzyjna i często stosowana w laboratoriach analitycznych do analizy skomplikowanych mieszanin chemicznych.
Jakie są przyszłe kierunki badań nad destylacją rozpuszczalników
Przyszłość badań nad destylacją rozpuszczalników zapowiada się obiecująco dzięki rosnącemu zainteresowaniu zrównoważonym rozwojem oraz technologiami przyjaznymi dla środowiska. W miarę jak świat staje przed wyzwaniami związanymi ze zmianami klimatycznymi i ograniczonymi zasobami naturalnymi, badania koncentrują się na opracowywaniu bardziej efektywnych procesów produkcyjnych. Jednym z kluczowych obszarów badań jest poszukiwanie alternatywnych źródeł energii do podgrzewania cieczy podczas destylacji, takich jak energia słoneczna czy geotermalna. Dodatkowo naukowcy pracują nad nowymi materiałami o wysokiej przewodności cieplnej i odporności chemicznej dla kolumn destylacyjnych, co może znacznie zwiększyć efektywność procesu. W kontekście ochrony środowiska trwają również badania nad metodami odzyskiwania i recyklingu rozpuszczalników po ich użyciu, co pozwoli na zmniejszenie ilości odpadów chemicznych oraz ograniczenie emisji szkodliwych substancji do atmosfery. Wreszcie rozwój technologii cyfrowych i automatyzacji procesów przemysłowych otwiera nowe możliwości optymalizacji procesów destylacyjnych poprzez zastosowanie sztucznej inteligencji i analizy danych w czasie rzeczywistym.
Jakie są kluczowe czynniki wpływające na efektywność destylacji
Efektywność procesu destylacji rozpuszczalników zależy od wielu czynników, które należy uwzględnić podczas projektowania systemu oraz jego eksploatacji. Przede wszystkim kluczową rolę odgrywa różnica temperatur wrzenia składników mieszaniny – im większa ta różnica, tym łatwiejsze jest ich oddzielanie podczas procesu destylacji prostej lub frakcyjnej. Kolejnym istotnym czynnikiem jest ciśnienie panujące w układzie; obniżenie ciśnienia pozwala na przeprowadzenie procesu w niższych temperaturach, co może być korzystne dla substancji termolabilnych. Ważne są także parametry przepływu cieczy i pary wewnątrz kolumny destylacyjnej – optymalizacja tych parametrów pozwala na zwiększenie wydajności separacji oraz poprawę jakości uzyskiwanego produktu końcowego. Również dobór odpowiednich materiałów konstrukcyjnych dla kolumny oraz innych elementów systemu ma znaczenie; materiały te powinny charakteryzować się wysoką odpornością chemiczną oraz dobrą przewodnością cieplną.